The packaging of sanitary napkins in manufacturing involves a series of steps and specialized machinery to ensure efficient and hygienic packaging processes:
- Stacking and Counting: Sanitary napkins are typically stacked and counted by automated systems before packaging. These systems ensure accurate quantities for each package.
- Film Unwinding: Packaging machines have rolls of film or wrapping material that are unwound and fed into the packaging process.
- Cutting and Sealing: Automated systems cut the film to the required size for packaging individual sanitary napkin units. The film is sealed or formed into pouches to enclose the napkins.
- Product Loading: The stacked sanitary napkins are loaded into the formed pouches or packaging material. This can be done manually or through automated loading systems.
- Sealing and Closing: Once the napkins are placed in the packaging, the machine seals the pouches or bags. Heat sealing, adhesive sealing, or ultrasonic sealing methods are used for secure closure.
- Quality Control Checks: Inspection systems verify that each pouch is properly sealed and contains the correct number of napkins, ensuring product integrity.
- Batch Coding and Printing: Machines often include modules for batch coding or printing expiration dates, lot numbers, or product information onto the packaging material.
- Trimming and Cutting: Excess material is trimmed off, sanitary napkin machine and the pouches are cut into individual units, ready for further packaging or bundling.
- Bundling or Cartoning: Packaged napkins may be bundled together in larger quantities or placed into cartons for shipment and distribution. This can be automated based on predefined settings.
- Final Inspection: Before the packaged products are sent for distribution, a final inspection may occur to ensure that all packages meet quality standards and are correctly labeled.
These packaging machines are designed for efficiency, speed, and precision, ensuring sanitary napkins are packaged hygienically, securely, and in quantities that meet consumer needs.
What steps are taken to minimize material wastage during production?
Minimizing material wastage is a critical concern in manufacturing, including sanitary napkin production. Several measures are implemented to reduce wastage:
- Optimized Production Planning: Detailed planning helps minimize material waste by precisely calculating the required amount of raw materials for production based on demand forecasts.
- Precision Cutting and Shaping: Advanced cutting and shaping mechanisms ensure precise cuts and shapes of materials, minimizing unnecessary waste during manufacturing.
- Automated Material Handling: Automated systems handle materials efficiently, reducing mishandling or damage that could lead to wastage.
- Material Recovery Systems: Some machines incorporate systems to collect and recycle excess materials, reducing overall waste.
- Adjustable Settings for Material Usage: Machines allow operators to adjust settings, such as material tension, speed, and cutting parameters, to optimize material usage without compromising product quality.
- Real-time Monitoring and Control: Continuous monitoring of production processes helps identify issues that could lead to wastage. Adjustments can be made promptly to rectify these issues.
- Trim and Edge Control: Systems are in place to control trim and edge materials during production to minimize unnecessary material loss.
- Efficient Rejection Systems: Machines have efficient rejection mechanisms to segregate defective products early in the production process, preventing further wastage downstream.
- Employee Training and Awareness: Training programs ensure operators understand the importance of minimizing waste and follow best practices to achieve this goal.
- Lean Manufacturing Principles: Adopting lean manufacturing principles, such as 5S (Sort, Set in order, Shine, Standardize, Sustain), helps in organizing the production floor for efficiency and waste reduction.
By implementing these measures, sanitary napkin manufacturers aim to optimize material usage, reduce scrap, and enhance overall production efficiency while minimizing environmental impact.
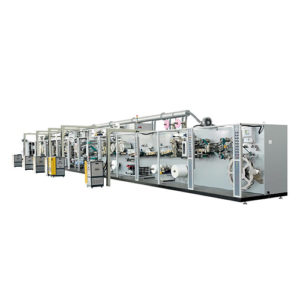